A sorter that removes foreign material and defects along with the core of iceberg and romaine improves product quality and food safety
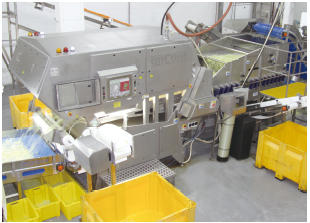
TRADITIONALLY, iceberg and romaine lettuces meant for bagged salads are manually cored in the field or in the plant. Manual coring causes excess product to be cut away to assure the core is fully removed and the highly nutritional outer leaves are typically discarded as well. Significant yield is lost, the nutritional value of the product suffers, and labour costs are high. A new integrated system, which combines a vibratory density separation shaker with a camera/laser sorter, eliminates manual coring to increase yields and improve product quality while reducing labour costs revolutionises the processing of iceberg and romaine lettuces in bagged salads. The system, 'onCore' from Key Technology, simultaneously removes foreign material and product defects from the production line, further improving product quality and food safety. Currently in use at leading fresh-cut produce processing companies in the U.S., Canada, and the U.K., onCore is driving a paradigm shift in how iceberg and romaine are processed. Eliminating manual coring and keeping the dark outer leaves remove less good product, which improves yields. The potential for labourers to inadvertently contaminate product is reduced and product degradation is slowed, thereby enhancing the quality of the product and increasing its shelf life. For romaine, a more uniform cut is achieved when whole heads are cut, thereby improving the consistency of the product. Product quality and food safety are maximised because the sorter removes foreign material and defects along with the core.
Two-step sorting process
With this system, the whole, uncored heads of lettuce are brought into the plant and cut using the same automated cutting technology that is traditionally used to cut cored heads of lettuce. After cutting, a two-step process removes the pieces of core as well as foreign material and defects from the product stream. First, onCore's three-deck Iso-Flo Density Separation Shaker uses gravity and directional airflow to remove 85 to 90 per cent of the core and spread product to present it to the downstream sorter. The effectiveness of this process reduces the volume of core being fed to the sorter, which helps the sorter focus on removing the smallest pieces of core along with foreign material and leaf defects. The second part of the process is the sorter, which can be designed using Key's Optyx or Manta sorter, depending on the necessary capacity of the line. The sorter is equipped with a combination of Key's Raptor laser technology and tri-chromatic colour cameras. The laser detects differences in the structural properties of objects to remove pieces of core and foreign material. The cameras determine each object's size, shape, and colour to identify and remove defects.
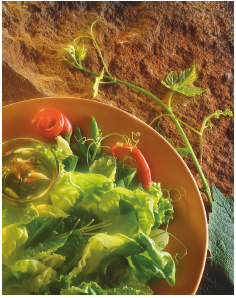
Ideal wavelengths - from infrared to ultraviolet - are identified for each application to accentuate the differentiation of good product from core, foreign material, and defects. Key then configures the sorter with the optimal combination of lights, lasers, and cameras to produce and capture the exact wavelengths that maximise the sorter's performance for the specific application. Using the small-volume Optyx 3000 series sorter, onCore processes up to 5000 lb (2268 kg) of iceberg or 4300 lb (1950 kg) of romaine per hour. For high volume lines, Key can design onCore using its Manta 2000 series sorter, which processes up to 16,000 lb (7258 kg) of iceberg or 14,500 lb (6577 kg) of romaine per hour. For mid-volume lines, Key's Optyx 6000 series sorter or Manta 1600 series sorter are ideal. Based on yield increases and labour cost reductions alone, onCore achieves a payback in four to 16 months. Improvements
Кроссовки Lifestyle