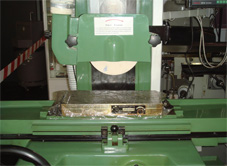
砂轮是用量最大、使用面最广的一种磨具,它使用时高速旋转,可对金属或非金属工件的外圆、内圆、平面和各种型面等进行粗磨、半精磨和精磨以及开槽和切断等。在使用频率如此之高的情况下,如何延长砂轮的使用寿命也成为使用者不得不考虑的问题。
Grinding wheels have two major components: the abrasiveg rains that do the actual cutting, and the bond that holds and supports the grains together while they cut. The percentages of grain and bond and their spacing in the wheel determine the wheel抯structure. Joint effort between management and staff can helpmaximize the life of your grinding wheels. Paying attention on the abrasives you抮e using and the metalyou抮e grinding to improve productivity can make life easier for theemployees assigned to use them. The abrasive used in a wheel ischosen based on the way it will interact with the work material. Thesuitable abrasive has the ability to stay sharp with minimal pointdulling. When dulling begins, the abrasive fractures, creating newcutting points. Each abrasive type is unique with distinct propertiesfor hardness, strength, fracture toughness and resistance to impact. Abrasives Aluminum oxide is the most common abrasive used in grindingwheels. It is usually the abrasive chosen for grinding carbon steel,alloy steel, high-speed steel, annealed malleable iron, wrought iron,and bronzes and similar metals. There are many different types ofaluminum oxide abrasives, each specially made and blended forparticular types of grinding jobs. Each abrasive type carries its owndesignation, usually a combination of a letter and a number. Thesedesignations vary by manufacturer. Zirconia alumina is another family of abrasives, each one madefrom a different percentage of aluminum oxide and zirconium oxide.The combination results in a tough, durable abrasive that works wellin rough grinding applications, such as cut-off operations, on a broadrange of steels and steel alloys. As with aluminum oxide, there areseveral different types of zirconia alumina from which to choose. Silicon carbide is an abrasive used for grinding gray iron,chilled iron, brass, soft bronze and aluminum, as well as stone,rubber and other non-ferrous materials. 