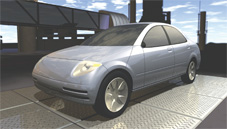
从半成品生产到生活消费品、军事硬件等制造领域,金属成型的使用范围已逾来愈广。本文将为您详细介绍金属板料成型在汽车领域中的应用。
Metal forming operation is a manufacturing process bywhich parts are fabricated from metal stock. It is the mostcommon materials processing steps in any industry, bothfor the production of semi-finished products, as well as for themanufacture of consumer goods and military hardware. The expenditure of capital investment in plant and operatingequipment for the production of goods is enormous. Sincethese operations occur within a high-volume industry, evensmall improvements in materials properties, simulations, andmanufacturing costs will translate into substantial savings. Major technological changes are on the horizon that requiresignificant advances be made in the science and technology of metalforming. These changes occur concurrently in basic materials and theengineering science of forming operations. One of these major changesis the reduction in weight for the next-generation of automobiles. Customers and government regulators continue to demandfor environmentally friendly, fuel-efficient cars. Of all the ways toincrease efficiency, weight reduction is by far the most effective.Automotive weight can be reduced by optimizing the design andusing a lightweight material. Aluminum is a good candidate for weight reduction. Itsproperties make it a versatile material for engineering andconstruction. It is light in mass, yet some of its alloys havestrengths greater than that of structural steel. Its specific gravity isabout 2.7. Its mass (weight) is roughly 35% that of iron and 30%that of copper. Commercially pure aluminum has a tensile strengthof about 13,000 pounds per square inch (PSI), so its usefulness as a structural material in this form is somewhat limited. Aluminum alloys have been considered for automotiveapplications, in particular for body panels. However, in comparisonto steels, aluminum sheet metal is more expensive and lessformable. The formability of the aluminum is directly related toits work hardening rate and level of anisotropy in its mechanicalproperties. These material properties depend on the alloyingcontent, preferred crystallographic texture, retained deformationmicrostructure, and/or re-crystallization microstructure followingprocessing. Thus, scientific advances in the prediction andcontrol of microstructures and textures during thermo-mechanicalprocessing of common aluminum alloys is the preferred route toobtain formability at low cost. Tool wear In automobile industries, sheet metal forming is widelyimplemented as an efficient deformation process to convert sheetmetal into various interior and exterior parts with prescribed sizesand shapes. A rapidly changing automobile market demands highprecision, perfect quality and a short lead time in the production ofautomobile parts. The tool wear of sheet metal forming dies is a majorobstacle for industries to meet these demands due to the introductionof many new types of steel and complex three-dimensional shape ofautomobile parts. Tool wear is a progressive damage to a die surface causedby relative motion with respect to a blank surface. However, due to the complicated geometric, material andnonlinear contact nonlinear characteristicsin the deformation of automotive parts, it isvery time-consuming and costly to predictthe tool worn area by means of try-outtechniques based on conventional trial anderror andAIr Jordan Outdoor Basketball Shoes