OHIO, USA-Milacron LLC, the global leader in high precision plastic processing technologies and control systems are pleased to announce that a partnership agreement has been reached with Trexel Inc MuCell? Microcellular Foam injection molding. The partnership agreement with Trexel will allow Milacron to incorporate the MuCell technology into their injection molding equipment offering.
Milacron is uniquely capable to provide the complete melt distribution and control solution for MuCell systems. The company’s extensive portfolio of primary processing equipment, combined with industry leading hot runner and control systems will allow MuCell technology to expand into new and untapped markets, according to Bruce Catoen, Milacron’s Chief Technology Officer. With Trexel as partner, Milacron has proven the viability of MuCell in blow moulding, co-injection, higher surface finish parts and high cavitation packaging applications. The light weighting, low tonnage, reduced warp and sink benefits of MuCell can now be exploited in markets that were previously not possible.
Under the agreement, Milacron will receive the rights to resell the Trexel MuCell SCF gas dosing equipment directly to their customers under the Milacron, Ferromatik, Uniloy and Mold-Masters brands while transferring the operating rights under Trexel’s patents to their end user without any added fees or costs.
Trexel MuCell foaming technology involves the introduction of precisely metered quantities of atmospheric gases (nitrogen or carbon dioxide) to create a foamed part, resulting in high quality precision and engineered plastic components, while greatly reducing production costs associated with lower material consumption, shorter molding cycle times, and reduced machine clamping tonnage requirements. For the automotive sector, the MuCell process enables component manufacturers to light weight plastic parts for overall vehicle weight reduction and improved fuel economy. The process also leads to predictable and repeatable part geometry, allowing for the use of lower cost polyolefin resins without warpage or distortion.
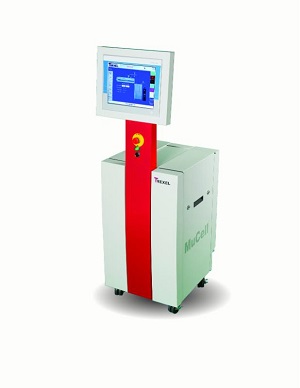