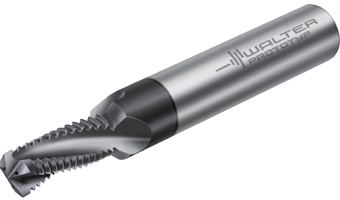
The Walter Prototyp TMD thread milling cutter which has been developed for aluminium and cast iron workpieces masters three separate processes: drilling, countersinking and thread milling.
Today's machining market demands shorter machining times and less unproductive downtime, and the automotive industry is no stranger to this. Automakers not only face a down economy, but also a competitive global market in which the parts that they need to machine, the machines used, and the materials they are machining are becoming more complex. Everyone knows the automotive industry must keep up with continual, radical change that includes: greater product ivi ty wi th higher quality, declining margins and higher precision, new materials, new locations and more demanding customers. Production is moving to different markets, and component materials are changing. With the different choices in milling cutters, how do you know which cutter is right for your cast aluminium or grey cast iron application. Choosing the right tool will allow you to use your machines' full capabilities, providing today's auto machinist with productivity and efficiency. Multi-functional tool solutions generate enormous savings, a single tool performs the same task that otherwise requires several. This means shorter machining times and less unproductive downtime. One such solution is the new Walter Prototyp TMD solid carbide thread milling cutter. The tool enables the complete production of internal threads ranging from M6 to M16 by combining the procedures for drilling, countersinking (90 degrees) and thread milling. The maximum standard thread depth is 2xD for both through hole threads and blind hole threads. The Walter Prototyp TMD has been designed for threads on cast aluminium and grey cast iron components. It is also suitable for magnesium and copper alloys in a secondary application. It is either used for drilling into solid material or into precast core holes. In order to ensure maximum tool life, the thread milling cutter is available with two optimised coatings, namely a TAX coating for cast iron and an NHC coating for non-ferrous metals. Three milling edges or three cutting edges, which are a special feature, ensure high chipping rates. A special spiral flute design with a 27 degree helix angle aids chip transport. Chip removal is supported by another important feature when producing blind holes in particular: a central coolant supply with three Y-shaped outlets. The steps required for thread production are as follows: 1. Position; 2. Drill and countersink; 3. Proceed to thread starting position; 4. Radial plunging to thread depth; 5. Counter rotation thread milling in the form of a helix; 6. Reset to starting position. As is the case with other tools of this type, the user receives the cutting data and the CNC programme together with the exclusive TEC-CSS expert software from Walter. The tool can therefore be integrated very easily into an overall process. The time reductions that can be achieved (50% is a realistic value) prove particularly advantageous in series and mass production, for example, in the automotive industry. A further advantage is the high thread quality. The positioning of the core hole for the thread is completely accurate. Optimum values are achieved for surface quality and tolerances in a process-related manner.(the end) Walter, Walter Titex, Walter Prototyp and Walter Valenite - four brand names under one roofAs a group of companies active worldwide, WALTER AG develops, produces and markets precision tools for the metal-machining industry. The four key brands of Walter, Walter Titex, Walter Prototyp and Walter Valenite are united under one company roof. The headquarters of Walter AG are in T黚ingen/Germany. There are a total of approx. 2,700 employees worldwide. ArounNike Shox Avenue 803