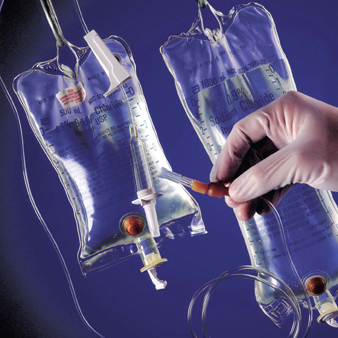
Thermorplastic elastomers (TPEs) are materials that have shown rapid growth in the past. More than anything else, TPEs' rubber-like properties as well as their processability have enabled the fabrication of increasingly complex parts with the use of more advanced machines, moulds and techniques. In the TPE Primer (ed. 2009), experts from ALLOD Werkstoff GmbH & Co, KG explained the basics of thermoplastic elastomers. The primer provides valuable guide on the design and processing of TPEs by injection moulding. TPEs emerged from the very first thermoplastic polyurethanes (TPUs) which were the first TPEs used in the mid-1950s for the production of elastic fibres and moulded parts by injection moulding. Next developed were the polyolefin blends based on ethylene-propylene rubber (EPR). Around 1975, styrenic block copolymers and thermoplastic vulcanisates were introduced. However, until the end of 1970s, TPE materials were only used in selected applications due to certain market concerns such as fears of contact. To date, TPEs have been used for various applications ?with the largest current market being the automotive industry, electronics/electrical, increasingly, the medical industry. Structural characteristics and uses of TPEs TPEs are comprised of a thermoplastic hard phase and of an elastomeric soft phase. Both phases, according to the TPE Primer, are thermodynamically fully or only partially immiscible and consequently act as two individual phases. The elasticity of the material is determined by the soft phase. The hard phase has the function of a "cross-linking site" and is responsible for the strength and hardness. In contrast to conventional elastomers this "cross-linking" is based not on covalent chemical bond but on the physical interactive forces. The reversible network resulting from the presence of the hard phase is the factor allowing the repeatable melting of the TPE materials. Briefly, a TPE can be characterised as follows: elastic and extensible with a low modulus of elasticity (depending on hardness); physical network soluble by suitable agents; thermoplastic processing; good ability to be combined with thermoplastics (multi-component technique); can be easily coloured, certain types of materials can be highly transparent; and use of regrind is possible. "The growth of TPEs in medical tubing sector stems from the materials' effectiveness as a replacement for traditional polymers" New areas of applications for TPEs have been explored in response to rising demands for higher resistance to temperature, enhanced elasticity as well as better chemical resistance. Custom-TPEs meet stringent rules PolyOne's GLS Thermoplastic Elastomers was awarded the Frost & Sullivan 2009 North American Plastics in Medical Tubing & Catheters Product Line Strategy of the Year Award. The award recognised PolyOne's continuous efforts towards innovative sustainable solutions for the medical industry. Walter Ripple, general manager, GLS Thermoplastic Elastomers, said, "Our R&D efforts include creating new compounds that address environmental concerns such as phthalates, while continuing to offer excellent performance and aesthetics. Our VERSAFLEX HC family of TPEs, made without phthalates or halogens, helps our customers meet performance, regulatory and environmental objectives." PolyOne's exceptional medical grade TPE technologies improve drug and fluid delivery systems. The growth of TPEs in medical tubing market stems from the materials' effectiveness as a replacement for traditional polymers. VERSAFLEX™ HC medical grade TPE offers customers a non-phthalate, halogen-free alternative designed to address this growing trend, providing a responsible option for a number of medical tubing applications such as IV catheters, peristaltic pumps, and surgical drainage tubing. ISO 10993-4 and 10993-5 certified, the Versaflex™ HC TPEs line includes grades f
Nike Air Max 90 Candy Drip