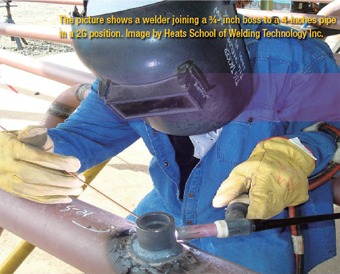
Welded pipes are manufactured from metal sheets formed in coils. The metal bends are hot rolled and coiled in circles. In this form they are placed in a magazine of metal sheets. The bends of metal sheet must be normalised and heat-plastic treated. The preparatory process must be agreeable with specified industrial standards and clients orders. It is important that all information about the raw material must be placed on each coil of metal bands. The main information described on the label includes: dimensions of a metal band, type of material and characteristics of plastic-heat processes. The coils of metal bands are transported using special trolleys. Each trolley must be operated by a crane. The transport system links a stacking yard with a production room. The end stations of the transport system are simultaneously the first stations of the main production process. In the production room the coils of a metal band are transported with a crane to the first stand to prepare them to the next phase of a technological process, where they are initially worked. The bends of a metal sheet must be uncoiled and straightened on the input stand. On this stand all uneven elements of metal bands are also cut. Cut elements are stored and transported on the scrap yard. The prepared metal bands are transported to the next operation stand. Prepared bands are joined by welding to obtain long bands and to allow pulling one band by another. The weld obtained in this phase is not controlled because, as it was stated, it has only the auxiliary role. When the pipe is finished this weld is cut out and scraped. The process of welding is conducted automatically. Bands' welding is needed to make possible the process of continuous pipes welding. Such prepared bands must be straightened because, during previous phases, it bends in a result of cutting and welding. This operation is conducted on a special stand consisted of many rows of rolls. A bend moving over these rolls becomes straightened as a result of influence of the gravity force. Straight bands must be still worked to prepare them for welding. The last preparatory phase is mechanical working. Welding process The process of pipe welding could be divided in three phases: a forming phase, a heating phase and a pressing phase. It is important to conduct all these phases precisely because the quality level of pipes is proportional to the exactness of coordination of all sub-processes. In the first phase, special rolls form the flat metal sheet into a cylindrical tube. It is a very precise operation because during this phase the pipes obtain their final shape. Next, the edges of a tube are heated by the inducting currents. These currents are generated using special impulse generator and ring inductor. The edges of the tube are heated up to the plasticization temperature. So it is controlled to heat only the edge of the tube because heating could results in changing the material parameters. Finally, the heated edges of a tube are clenched to obtain the pressure weld. The characteristics of a weld strongly depend upon the clenching operation. The most important parameter is the leak tightness of a weld. The presented pressure welding technology is characterized also by some economic advantages. Firstly, it is not generated the waste material during this process. Secondly, the pipes could be produced continuously so it is possible to increase the productivity factor of this technology. As it was stated the process of heating is related with the density of inducted currents of high frequency. To increase the concentration of a magnetic field in the welding area, the special magnetic resistor is used. And this resistor is placed inside a welding pipe.(the end)
Vêtements et équipement Lifestyle pour Femme