快速制模(R T)技术将传统的制模方法与快速成型技术相结合,以满足模具制造商对缩短周期、降低 成本、提高精度、延长模具使用寿命等方面提出的要求。本文还将为您介绍速度快、无污染、低成本的熔 丝沉积成型(FDM)以及应用于汽车制造的铝质模具。
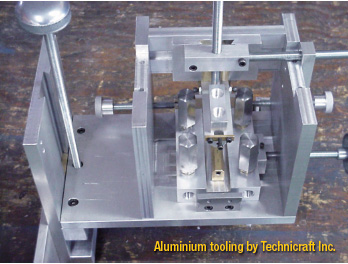
Rapid tooling (RT) is using a rapid prototype, either indirectly or directly, as a tooling pattern for creating a mould. It enables you to have moulds that supply prototype parts with the correct material at a substantially reduced cost or in a fraction of the time it takes to produce parts from production tooling processes. Rapid tooling can also mean using additive technology to make production tools-not just moulds, but custom or short-use fixtures and assembly tools. Both RT types are becoming increasingly popular, with numerous developments happening in both creating moulds and using additive technology. Developments in rapid tooling make this technology even more attractive for quick, low-cost, customisable, and even environmentally aware manufacturing. The "rapid" in rapid-tooling technology originally meant that moulds could be made much faster than with conventional machining. That's still true. But in the last few years, RT technology has evolved toward building moulds that provide up to 40% faster cycles than are possible with conventional technology. That emphasis on productivity accompanies a shift in RT applications from prototype to full production tooling.
Higher productivity moulding Newer RT approaches can minimise or eliminate warpage and internal stresses caused by uneven cooling while boosting productivity by drawing heat more quickly from thick sections or other hard-to-cool features in the mould, such as bosses or ribs. Tests of newer high-conductivity tools by at least two sources reportedly found that cooling time in the moulding cycle could be set to zero and the process would still yield acceptable parts. Conventional tool making is limited by the modest thermal conductivity of standard tool steels like H-13, P-20, or stainless, which are chosen for hardness and/or corrosion resistance. Cooling is also limited by reliance on straight gun-drilled channels in the mould base. Conventional mould makers can attempt to overcome these limitations with inserts of beryllium-copper or other highly conductive copper alloys, secondary cooling channels or "bubblers" in deep cores, and heat pipes or "thermal pins" that can reach into the body of the tool to extract heat. Suppliers of rapid tool making techniques have developed two routes to improved mould cooling: building conductive metals into the tool from the start and/or incorporating cooling channels that conform to the part surface, no matter how irregular its shape. RT suppliers claim that either or both of these methods can do better than either bubblers or heat pipes. And the newer RT methods typically combine conductive metals with a tool steel to create a bimetallic structure that helps deliver better wear resistance than copper alloys or aluminium alone.
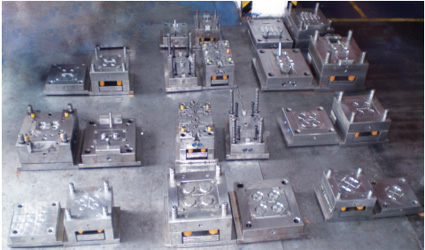
Some conductive alloys for conventional mould making have hardness values as high as 30 to 40 Rc, similar to P-20 steel. There are also methods of prehardening coppe
New Balance