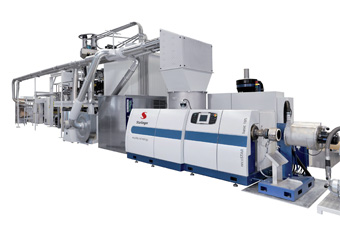
The latest developments in the field of efficient and economic plastics recycling are expected to serve as highlights in some of the K 2010 exhibitors' booths. One company, EREMA, the Austrian recycling system specialists, is set to launch its new TVEplus recycling system. As a next-step development of the proven TVE extrusion system with high-performance degassing for difficult recycling jobs, the degassing and homogenisation performance of the TVEplus has been considerably enhanced. This system also includes new and improved downstream components in terms of technology, maintenance and cleaning from the hot die face pelletiser to the drying centrifuge. With the fur ther development of the TVE ext ruder configuration with the melt filter upstream of the melt degassing extruder section to form the TVEplus technology, even extremely difficult waste materials - including full-surface and multilayer printed packaging films that are increasing in use - can be processed in a single pass to produce high-grade recycled pellets. Binding agents and contaminates that are always contained in the inks are particularly problematical as they previously only partially broke down at the processing temperatures of the plastics matrix and could not be efficiently removed in the extruder degassing zone. New design features on the TVEplus extruder, in particular the new extruder screw mixing zone which is situated between the melt filter and degassing station for the melt, ensure that both processing and the degassing of the melt are now highly effective. The filtration performance is also increased due to improved extruder screw design and allows for lower melt temperatures, making it extremely material friendly while achieving higher throughputs at the same time. Further developments also open up extended possibilities for the VACUREMA technology, especially when processing PET bottle flakes to produce rPET that is suitable for food contact as documented by many national and international certification organisations. The newly developed, compact, space-saving inline crystalliser, for example, enables processors to keep to a reliable acetaldehyde (AA) content of under 1 ppm in the recycled PET pellets. The required IV value, according to the application, can be achieved flexibly in the process through the modular VACUREMA concept with the Basic, Advanced and Prime (IV values similar to virgin PET) technology phases. All EREMA recycling systems continue to feature the ecoSAVE technology introduced earlier. This reduces the already very low specific energy consumption of this recycling technology by up to an additional 10%. Processors not only save energy costs, but they also play an active part in climate protection by further reducing CO2 emissions.
Processing diverse materials
Another company that will present its recycling technology is Starlinger & Co GmbH. Starlinger's product range of recycling technology comprises innovative machine solutions for efficient recycling of plastic materials such as PE, PP, PA, PS, PET and many others. This year at K, three Starlinger recycling lines will be on display. A recoSTAR universal 65 VAC with an output of up to 200 kg/h will be in action processing PP sack fabric. This machine is equipped with a heavy-duty single-shaft cutter arranged parallel to the extruder, making it possible to easily process also films and hard-to-grind materials such as tapes, fibres and start-up lumps. With the line's new feeding system, both ground material and granulate can now be processed without requiring an additional dosing unit. Further more, this new feature increases operational reliability, simplifies operation and ensures lower energy consumption and higher output at the same time. Compared to other processes, the recoSTAR universal produces regranulate that is for instance, less dis
Air Max