A complete weighing and packing line helps a smoked fish specialist to meet growing demand for salmon lardon
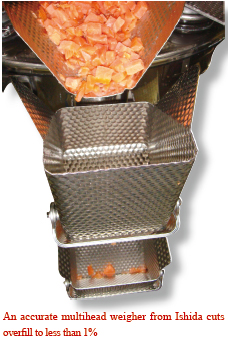
SMOKED fish specialist Meralliance has been able to reduce product giveaway whilst enhancing pack presentation of its salmon lardons in retail outlets. The seafood processor of Quimper in the French region of Brittany achieved this by switching to an automated weighing and packing line that met three key objectives: avoid overfill-a phenomenon that is inevitable with manual packing; improve working conditions; and offer retailers the best possible pack presentation. Smoked salmon lardon are small cuts of fatty salmon that were developed by Meralliance as a speciality product from its annual volume of 4,500 tonnes of smoked fish. The ingredient is growing in popularity as an extra touch of quality and flavour in pasta, salads, quiches, soups, kedgerees and many other dishes. Before the installation of the new line the salmon lardons were weighed out and manually placed on the infeed conveyor of a thermoformer. This laborious approach was fast becoming a limitation and the company sought to automate the process in order to meet three key objectives. "At the end of 2007, given the growing success of this product with the large and medium supermarkets, automating the smoked salmon lardons line became an obvious step," explains Meralliance industrial director Vincent Gélamur.
Meeting the objectives Ishida Europe was selected for the installation from five potential suppliers, due to its ability to offer a complete line solution that met Meralliance's objectives. Today, the chilled smoked salmon is diced, sorted on a vibratory conveyor and conveyed by vacuum direct to the dispersion table of a multihead weigher. The weigher is a 10-head model of the Ishida RS-Series, equipped with a powerful product feed / vibratory system. However, despite its high (14-18%) oil content, the salmon is not as sticky as might be expected, owing to the fact that it has little time to warm up in the fast vacuum transfer from the cutting to the weighing station. Trays are denested and conveyed to an Ishida distribution system, where each receives its portion from the weigher. Next, the trays pass through an Ishida QX-775 Tray Sealer, where they are nitrogen flushed and sealed. Tray format (147mm x 113 mm x 18mm) and portion size (90g) are such that each pack is quite full, a challenge which the distribution system and the QX-775's sealing system are able to meet very effectively in order to satisfy Meralliance's pack presentation requirements.
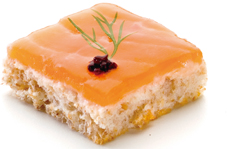
Avoiding overfill. The accuracy of the RS-Series multihead weigher, which stems from Ishida's latest combination calculation hardware and software, is such that giveaway has been sharply reduced: overfill is now less than one per cent. Improved working conditions. Operation of the system is simple with clear intuitive graphics. As well as eliminating the manual filling operation, the system offers easy cleaning with the waterproof weigher featuring lift-off, drop-on contact parts, whilst all product feed areas of the tray sealer are accessible for washdown. Better pack presentation. The packs, which have a 6-day shelf life, are displayed standing on edge on the supermarket shelf. If they were not so generously filled and securely sealed, settlement would soon leave them looking under-filled. The neat inside-cut seal delivered by the QX-775, which also equips the packs with an easy-peel facility, further enhances pack presentation. Meralliance is delighted with the installation. "Three and a half months after the order was placed, the line was producing 1800 trays per hour, and is capable of up to 3600," says Mr Gélamur.(the end)
adidas Laufschuhe und Laufbekleidung kaufen