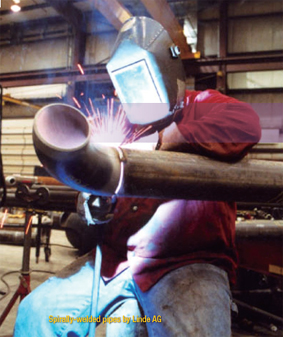
The reel-lay process is one of the most effective offshore oil and gas pipeline installation methods for pipes ranging from 3 to 16-inches in diameter. To date, most of the pipe has been seamless line pipe; however, welded pipes can also be reeled. In particular, high-frequency induction (HFI) welded pipes can be manufactured in the sizes currently suitable for reeled applications and have already been proven in numerous projects. HFI-welded line pipe offers benefits over seamless pipe in terms of improved lead times, lower project costs, tighter dimensional tolerance and good control of mechanical properties and chemistry resulting in excellent weldability. HFI pipe is cold formed from steel strip using a series of forming rollers. The manufacturing process then involves 'inducing' a current into the edges of the strip with the use of an induction coil. The HFI fusion weld is created with no filler material and there is no direct electrical contact in the process. The HFI manufacturing process produces a pipe with the following attributes resulting from the control of coil feedstock dimensions. The alternating current induced within the steel strip after forming, concentrates in the surface of the strip edge due to the skin effect. This generates heat that fuses the strip edges together. The benefits of HFI versus seamless and the forming process: * Consistency of wall thickness along the pipe length * Consistency of outside diameter * Low levels of out of roundness in entire pipe body * Little or no weld bead--no weld filler material * High levels of weld integrity, toughness and strength HFI pipe advantages Conventional design codes for reeling pipe have been constructed using the typical properties of seamless materials, however, HFI pipe has different properties which must be taken into account when used for HFI reeling applications. The current seamless-based specifications fail to address the geometrical and mechanical properties that need to be considered when comparing these two materials, e.g. how the improved tolerances facilitate use of reduced wall thicknesses. It is also important to understand how the HFI pipe responds to the plastic deformations that occur during the reeling process, both in the base metal and fusion line regions of longitudinal seam weld. HFI pipe is attractive to installation contractors and operators as it can significantly reduce the unit cost of large-scale, longdistance pipeline projects. HFI pipe is generally less expensive per ton than seamless pipe and its specification can offer additional savings. By virtue of the tighter dimensional tolerances achievable with HFI, the nominal wall thickness of the pipes can be reduced, providing additional material savings and potentially reducing welding, inspection and repair time for the pipeline. Another potential advantage is the ability to supply in longer lengths. Reeling impact on steel pipe During the reeling process, the pipe must be able to withstand strains arising from the bending moment; the axial load applied by the tensioner, as well as contact loads with the pipe reel and straightener without buckling or failure. However, the bending moment remains the primary loading mode, controlling mechanical behaviour of the pipe during reeling. The stress-strain history is different for the intrados and extrados positions of the pipe reel. In the intrados the material is first subjected to compression before experiencing tensile strains during reeling-off and straightening. The opposite combination occurs within the extrados location.(the end)
Air Jordan VII 7 Retro