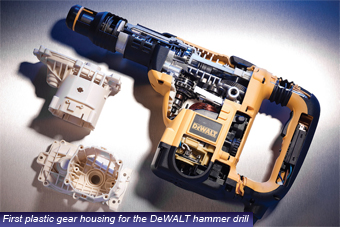
The new hammer drill made by DeWALT - a worldwide developer and manufacturer of professional power tools and part of the Stanley Black & Decker corporate group - has a plastic housing that is a combined part, enclosing both the electric motor and the gear. The engineering plastic used here is BASF's Ultradur® B4300 G6. The new power tool has been introduced by DeWALT retailers in Switzerland in June with commercial sale throughout Europe before the end of this year. The sophisticated part inside the power drill replaces two separate housings, one of which - the gear housing - used to be made of die-cast magnesium. The new plastic housing now accommodates the electric motor and the gear along with the chain drive; consequently, it has to be dimensionally accurate and ensure that the axes of the gear components are parallel and that they remain so, even at high operating temperatures. BASF's PBT Ultradur B4300 G6 provides the requisite stiffness and dimensional stability, even in a humid environment. The very good flow properties of this plastic make it easy to create filigree contours and, not least of all, to reduce the weight of the hammer drill when compared to the version with the metal housing. This is the first time that DeWALT is using PBT in such an application. According to Mr. Reimund Becht, project manager at DeWALT Professional Engineering in Idstein, Germany, Ultradur plastic offers the classic advantages of this class of materials. "Doing away with an additional metal part simplifies inventory and logistics, while the integration of key functions such as snap-on fastenings eliminates the need for screws and cuts down on assembly time. Moreover, there is no longer a need for cut threads and the cost for parts is reduced since plastic parts are very precise and, in contrast to metal, do not have to be mechanically reworked." Additional electric insulation of the live parts of the motor can also be dispensed with, so that the entire construction becomes more compact. Finally, the acoustic damping behaviour of this plastic is fundamentally superior to that of metal, and the injection mould lasts longer than the magnesium die-casting mould. DeWALT also makes use of BASF engineering plastics in other special applications in the new hammer drill: Ultramid A3WC4, a BASF carbon-fibre-reinforced polyamide, is employed for the very rigid connecting rod, which joins the piston to the crank wheel. The yellow and black exterior housing parts are made of the especially impact-resistant Ultramid B3ZG6, whereas the components situated close to the motor that come into contact with hot and live parts are made of Ultramid A3EG6 or Ultramid A3EG7. DeWALT itself manufactures the plastic parts of the new drill hammer at its plant in Usti/Trmice (Czech Republic). Ultradur® is BASF's brand name for its line of partially crystalline, thermoplastic, saturated polyesters derived from polybutylene terephthalate (PBT). They are employed as materials for high-quality technical components in many sectors of industry. The material is highly stressable with high rigidity and strength, while possessing very good dimensional stability under heat. It maintains good resistance to many chemicals and shows exceptional resistance to weathering and with excellent heat ageing behaviour. The most important applications of Ultradur® are automotive engineering, electrical engineering, electronics and telecommunications as well as precision engineering and general mechanical engineering. As a general rule Ultradur® can be processed by all methods known for thermoplastics. The main methods which come into consideration, however, are injection moulding and extrusion. Complex mouldings are economically manufactured in large numbers from Ultradur® by injection moulding. The extrusion process is used to produce film, semi-finished products, pipes, profiled parts
Lebron XIII Elite PE