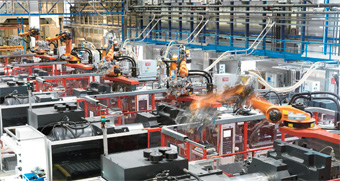
Located in the tranquil village of Assamstadt in the north of Baden-W黵ttemberg, Germany, Magna Spiegelsysteme produces interior and exterior mirrors for the premium manufacturers of the German automotive industry. If you drive a Mercedes, BMW, Audi - or a Porsche - then you will have glanced countless times into an exterior mirror that was made at Magna in Assamstadt. Magna Spiegelsysteme in Assamstadt belongs to Magna Mirror Systems, a subsidiary of the leading global automotive supplier Magna International Inc. The range of products developed and manufactured by Magna Mirror Systems includes interior and exterior mirror systems, electrochromic glass, actuators, camera vision systems and door handle systems. An impressive total of 14 million plastic parts leave the plant every year. The complex removal process for the high-quality plastic mirror housings is entrusted to KUKA robots. "Magna Mirror Systems is a global supplier to the automotive industry and one of the largest producers of car mirror systems worldwide," explains Mr. Ralf-Peter Hericke, Head of Injection Molding at Magna Spiegelsysteme in Assamstadt. Since 2007, Magna in Assamstadt has relied on the competence and flexibility of KUKA robots for demoulding and packaging operations: shelfmounted robots of type KR 60-4KS and variants from the KUKA product range, which are ideally adapted to the complex removal process with their optimised reach, weight and acceleration.
Degrees of freedom Removal, weighing, cutting and packaging - this is the complicated constellation of tasks to be handled after the injection moulding of a mirror housing at Magna. The decision-makers in injection moulding had the idea of using jointed-arm robots for the complex removal operation. Previously, the parts were demoulded in twos or fours using a linear robot and set down on a conveyor system. The automation solution from the Augsburgbased technology leader gives Magna more degrees of freedom than conventional handling equipment. "That is a big advantage, especially when switching products," says Mr. Hericke. "The online monitoring, the 100% weighing check, and the possibility of implementing any reworking of the parts within the creation process itself - all this is accomplished by the KUKA robots", says Mr. Gerhard Leutwein, process engineer in Injection Molding.
Elegant solution for complex processes For the production of a mirror housing at Magna, plastic granulate is first melted in the screw chamber of the injection moulding machines and injected into a closed mould. The product must then cool in the mould. The ejectors move the part into the removal position, at which point the KUKA "Speed" robot KR 60- 4KS comes into play: equipped with a removal gripper from KUKA system partner SAR, the robot demoulds the product, moves it out of the machine area, cuts off the various sprues and sets the mirror housings down in pairs on the scales. After the weight check, defective parts are separated out straight away. If the product passes the quality check, it is immediately packed in a box by the KUKA robot. Where necessary, the KR 60-4KS also inserts a slipsheet to protect the high-quality mirror housings during transportation. "With a linear robot, it would not have been possible to implement the entire process," says Mr. Hericke.
Space-saving concept,short cycle times The limited space available was a major consideration for Magna: "We save a huge amount of space because we can install the KUKA robots as shelfmounted robots on the non-operator side of machine," explains Mr. Leutwein. This compact mounting arrangement allows the injection moulding machines to be installed very close together; the space requirements for the peripheral equipment on the non-operator side of machine have also been optimised. These
Nike