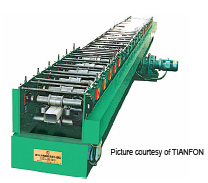
Oil producing countries in the Gulf region are expected to spend about US$50 billion in 2010 to increase their current oil field production capacities or to develop new discoveries. Thus, steel tube and pipe production is anticipated to a large increase over the next decade. Roll forming can be a versatile process in producing steel tubes and pipes. Roll forming the tube is described best as a progressive edge form, high oval without idlers. The strip is formed from the outside using an over formed radius on the first pass of about 15 degrees. The second pass forms the next 15 degrees, allowing the first pass work to relax, and then continuing using this type of forming method, allowing the high oval to stay in the sides. Roll forming supplies pressure in the vertical plane only, and the tooling must be designed with this in mind. Rolling uses an appropriate size die that adjusts to the steel tube. Pressure is applied as the material passes through the machine to bend the tubing or the beam to the desired radius. Roll forming is effective when the material must be bent a great deal, it can produce bends up to 360 degrees. This method is ideal for producing steel coils or to bend tubing for spiral staircases and the like. Because rolling requires fewer set-ups and uses pre-made dies, the cost is less than other ways to bend and form steel. Advantages of metal roll forming over traditional pipe, tube making Roll forming, sometimes also termed open section forming, employs a series of sets of dies in order to bend a sheet of metal little by little until the desired profile (cross section) is obtained. Roll forming is a continuous operation of bending in which a long metal strip or sheet- usually of coiled steel - is passed through sets of rolls or stands, each of which performs only a small incremental portion of the bend until the finished cross section profile is achieved. Roll forming is especially useful in the production of parts of long length, and in large quantities. Metal roll forming is quite like traditional pipe and tube making. However, roll forming is able to create more complicated profiles. In both pipe and tube making and in roll forming metal sheets are bent with roller dies, in which each roll pair works the sheet progressively until the final shape is obtained. Roll forming differs from the older techniques in that it can be combined with pre-punching, post-punching, and midpiercing inline, together with sweeping prior to cut-off. Special processes Like tube and pipe mills, roll forming works with all metals, both ferrous and nonferrous. Stainless steels, martensitic steels, high-strength low-alloy steels, and aluminium coils can be roll formed. Steel and aluminium coils sometimes are embossed with wood grain finishes, such as for garage doors. When embossing, the depth of the embossment must be considered so that the roller dies do not roll the embossment back out. Pre-painted and even vinyl-laminated steels can be roll formed but not welded. Tubing from prefinished materials is usually formed with a lock seam. A lock seam requires knurling the edge of the strip, either in the flat or elsewhere in the forming process, then making the opposing hooks and forming the tube, which is run over a mandrel to lock the hooks and then cut off. Roll forming is a versatile process that allows design innovation. Setting up a roll forming line requires the expertise of a skilled roll form designer and cooperation between the vendor and manufacturer in developing a successful product. Carefully choosing the proper equipment, skilfully designing the product and tooling, properly training the operators, and adequately maintaining the production line make roll forming easier.
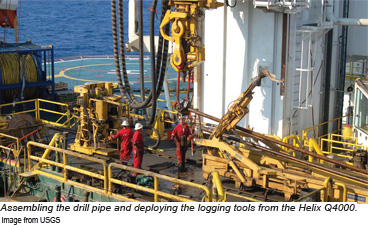
Material deformation in bending Roll forming induces two major types of deformation: transverse bending and
Alle Artikel