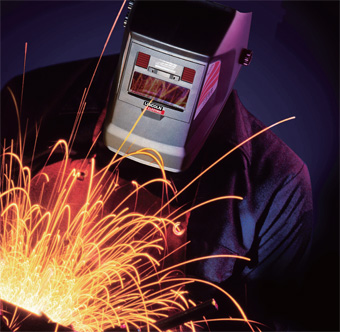
Welding technology has evolved dramatically over a period of time, thus the need for skilled welders is greater than ever. Today's welder must be proficient in multiple welding processes. At the very minimum, he or she must be able to weld all manner of piping using the manual SMAW and GTAW processes, but the necessary skills sets do not stop there. Welding is what holds the majority of structures together--bridges, cars, tractors, cranes and buildings. If any engineer does not have a good understand of this very popular joining process major problems can exist, such as failures from designing a joint that is un-weldable. Most companies these days are trying to hire welding engineers to help with these problems. Welding can get very specialised with more technical metals and applications. Training for welders should include a variety of automatic and semi-automatic orbital welding processes. These are necessary skills for meeting the stringent demands of the high-purity piping industry. High purity is an industry within our industry developing out of the manufacture of computer chip and pharmaceutical products. Orbital processes are becoming the preferred method of welding on pipelines, heavy industrial plants, such as chemical and refining operations, and also nuclear and conventional power production plants. It is becoming commonplace for welders to operate semiautomatic welding equipment remotely. This is done through the use of modern fibre-optic cameras allowing the welder to watch the welding operation on a video monitor. As an example, this process is used in nuclear plants during intensive welding operations during steam generator change-outs, or for re-piping projects in highly radioactive areas. The remote operation of the welding equipment limits exposure to radiation.
Skilled labour shortage Today's need for highly trained welders is compounded by the fact that the construction industry is experiencing a skilled worker shortage - and predictions reveal it may get worse. The Bureau of Labour Statistics (BLS) states that the average construction worker is 47 years old, and as aging baby boomers retire or leave the industry, they take much-needed skills with them. The Bureau of Labour Statistics estimates that the construction field will need to attract 240,000 workers each year to replace those leaving the workforce, while still allowing for industry growth. BLS statistics also reveal that 450,000 welders will be needed nationwide by 2014. To find enough individuals to fill that tall order, the construction industry must turn its attention to recruitment and extensive training. The recruitment process must examine and reach out to those segments of our country's population which have experienced alarmingly high levels of unemployment. There are many thousands of Americans who have not yet found careers that match their talents or meet their needs. They look forward to the day when they can find fulfilling employment that will enable them to earn a decent living. It's all a matter of connecting the right people with the right jobs - and the right training. Some welders become certified, a process whereby the employer sends a worker to an institution, such as an independent testing lab or technical school, to weld a test specimen according to specific codes and standards required by the employer. Testing procedures are based on the standards and codes set by one of several industry associations with which the employer may be affiliated. If the welding inspector at the examining institution determines that the worker has performed according to the employer's guidelines, the inspector will then certify the welder being tested as able to work with a particular welding procedure.(the end)
Air Jordan V High Supreme