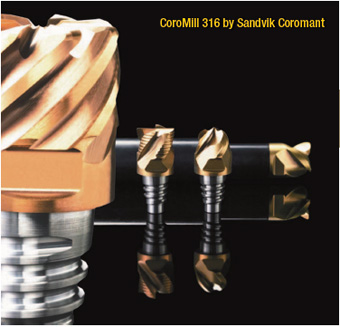
Selecting the proper tool holder is a requirement for a successful machining, since it has a great influence on the results of completing the machining process; especially with the levels of precision and accuracy required in today's market. The tool holder is an important connection between the machine spindle and the cutting tool. Tool holders are mainly purchased at the time the machining centre is bought, so tool holder manufacturers often follow the sales trends of the machine tool builders. Though the market contains many systems varying in holding power, price and flexibility for a tooling device to become a suitable solution, many buyers face common dilemmas of choosing more than what they need or insufficient of what they require.
Integrated tool holders Sandvik Coromant recently released a new range of integrated tool holders designed for compatibility with CoroMill 316 exchangeable-head (EH) tools. The holders achieve a secure performance better than a cylindrical shank clamped in a precision chuck, with comparable tool overhang, regarding torque transmission, run out and accuracy. For best overall machining results, tool overhang should always be kept to the absolute minimum. Integrated holders with an EH coupling provide a shorter total programming length compared to cylindrical shank tool holders with EH coupling. Integrated holders therefore provide the highest stability, when all other machining variables are the same. With modular tooling possibilities the holders can be used in many tooling combinations to suit application and machine tool, from a smaller inventory of standard items. For greater tooling flexibility these holders reduce set-up times, require minimum adjustment of tool length for each application and a stable performance is always guaranteed.
Collet chucks For many years, collet chucks have been popular because of their low pricing and have been the established tool holders for many machining applications. Unfortunately, the same scenario happens in many companies: Because of worry over loose tools, many machine operators are tightening the coolant tube nut of the collet mountings with oversized extensions. They also have to repeatedly clean the dirty components of the multi-part tool holders and be aware of how fast the tools wear in the collet mountings. Because of this, experts agree that precision tool holders offer enormous potential concerning quality, performance, process reliability, and lower costs. Investments in modern tool holders generally pay for themselves in a very short time and ensure future competitiveness in metal-cutting manufacturing.
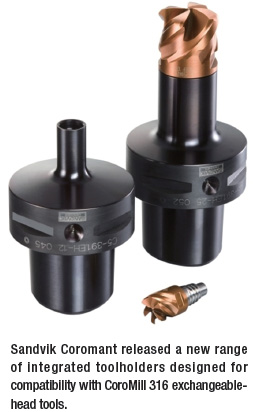
Two strong arguments for precision tool holders: quality demands of customers and cost calculation. On one hand, tolerance allowances of modern workpieces become better, on the other hand, cost is increasing, which makes it necessary to maximise profit in all areas of productivity. At the very least, when the operator is thinking about automated manufacturing, a higher efficiency or the use of high-quality tools, the tool holding equipment has to be critically analysed.
Advantage of damped expansion tool holders In case of rough machining, not only a tight and safe hold of the tool is important, but also are the dampening characteristics of the tool holder. When the tool edges are immerging, vibrations of the tool are generated, which can spread out over the whole machine tool. If these vibrations occur in the right frequency, the frequency of the machine, the vibration can become very strong and damage the tool. Expansion tool holders offer secure clamping and excellent dampening characteristics. The oscillation amplitude considerably reduces vibration and the surface becomes smoother instead of rough and bumpy. By avoiding highoscillation amplitude, the load of the
Nike Shox Current 807