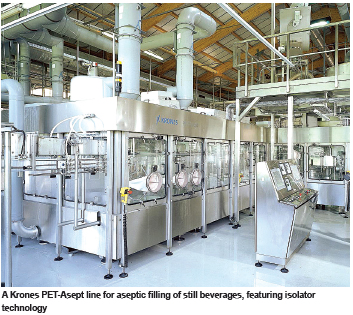
IN the soft drinks sector, choosing the right filling system means meeting requirement profile of the filling job in order to avoid performance- and quality-related problems. In addition, cost-efficiency aspects like change-over times for different products and container formats have to be taken into due account, so as to minimise standstill times and upgrade overall line efficiency. Today's increasingly stringent hygiene requirements also contribute toward continual optimisation of existing filling systems and the development of new ones. Krones has long since opted for flow meter technology in the field of aseptic filling, in which still beverages can be filled in non-contact mode, or their carbonated counterparts (like spritzers) in a counterpressure process, with the bottle pressed against the filling valve. Basically, most of the commonly produced beverages can be bottled using flow meter technology. Carbonated soft drinks and still beverages, aseptic PET bottling, but also hotfill processes in PET bottles, are likewise possible, as is can filling, provided the beverage involved possesses a minimum level of electrical conductivity. For products with little or no conductivity, or beverages with a high content of pulps, fibres, fruit chunks or fat, gravimetric filling can be utilised as an alternative, with the flow meter being replaced by an electronic weighing device. Modern-day monobloc solutions The advantages of blow-moulder/filler monoblocs compared to traditional line concepts are a substantial reduction in capital investment costs - savings in terms of bottle conveyors and buffering systems - go hand in hand with stringent savings in operating media and energy. At the same time, the footprint required by monobloc-synchronised machines is significantly smaller; this is crucial in the event of capacity upsizing and what are often severely restrictive space constraints. The close proximity of the two reference machines in a line, moreover, enables one machine operator sufficing for both the blow-moulder and the filler. The line's efficiency is improved by the elimination of components susceptible to malfunctions, which leads overall to reduced downtimes and, with the advantages outlined above, to substantially lower production costs.Monobloc solutions can be used for practically every PET filling job. Still products can be handled just as effectively as carbonated beverages or hot-filled drinks. It may be necessary to cool the hot PET bottles arriving from the blow-moulder before they are filled. There are various options available for this purpose, with Krones opting for simple, affordable water-cooling. Only about 2ml of water are required per bottle. There is also an option for integrating units for bottle sterilisation in the monobloc, which opens up additional possible applications for monoblocs in the fields of EHF (enhanced hygienic filling) and aseptic filling. Increased demand for hygiene Hygienic, aseptic filling technology is increasingly preferred to cold sterilisation or hotfill methods. Modern-day filling plants frequently operate with cleanrooms, designed to provide protection against microbiological re-contamination of the product during the filling process.
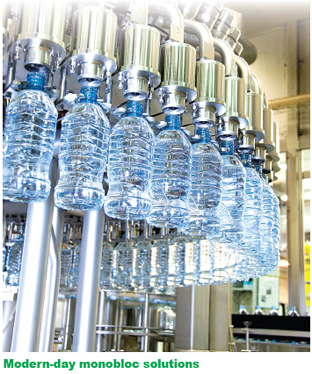
For highly sensitive beverages, like still juice drinks and near-water products without any carbonation, only an aseptic isolator-based design is able to provide the requisite microbiological safety. A Krones PET-Asept line for aseptic filling of still beverages, featuring isolator technology Here, all the crucial areas, from bottle treatment all the way through to the discharge conveyor, are enclosed in a stringently monitored sterile cleanroom atmosphere, the isolator. The isolator's surfaces are cleaned and sterilised using integrated jetting systems connected to the hygiene centre. To enable op
Zoom Lebron XI 11