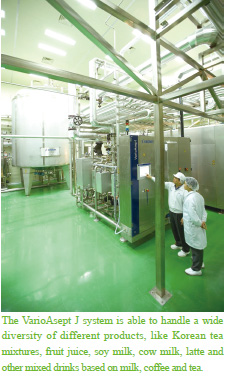
Co-packaging for aseptic products
In 2007, at its facility in Kwanghaewon, Hyosung Packaging took its first step towards co-packaging for aseptic products by commissioning its first aseptic bottling line for tea, tea-based mixed drinks, latte and other milk-based mixed beverages, which with their low-acid pH value react with particular sensitivity to microbiological spoilage. Kwanghaewon plant manager, B. K. Lee, recalls that Hyosung was the first company in South Korea to tackle aseptic filling of sensitive beverages at a time when the preferred option was for hotfill. "Aseptics is much gentler on the products, and preserves the vitamins more effectively, that's something we have to get across to consumers in South Korea," said Mr Lee. In order to communicate the differences between aseptic and conventional filling, and to highlight the advantages of aseptics, Hyosung simultaneously launched the new "Asepsys" logo on the Korean market, which appears on the labels of the beverages bottled using this method.Independent UHT system
Because this new line of business proved successful right from the start, Hyosung Packaging commissioned a second aseptic line from the same Japanese manufacturer at the beginning of 2010. This time, however, they opted for an aseptic process zone from Krones AG, enabling the German beverage technology supplier not only to supply its first aseptic UHT system to Korea, but also to place its first stand-alone UHT system worldwide that's not linked to the installation of an aseptic filling monobloc. The system comprises a VarioAsept J with the following modules: media interface, deaerator, homogeniser and shell-and-tube heat exchanger, plus a VarioStore aseptic buffer tank, which holds the UHT-treated beverages in readiness upstream of the filler. As a whole, the system has been designed for a maximum output of 24,000 litres an hour depending on the viscosity of the product involved, however, the output can also be reduced to as little as 9,720 litres an hour, which gives the system great flexibility.Significantly reduced product losses
A collecting system for mixed phases, the integrated buffer tank, plus automatic output adjustment from 100 to 40 per cent of the rated figure, all help to minimise product losses and maximise cost-efficiency in the event of fluctuating production at the upstream or downstream systems. "At the phase change between product and water, particularly, Krones' system ensures significantly lower product losses than we used to have. We're confident of dramatic savings, down to a third of the previous losses," said Mr Lee.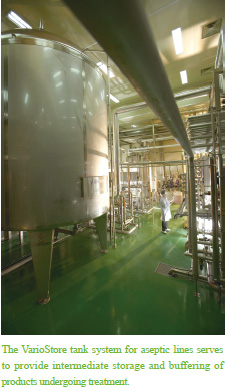