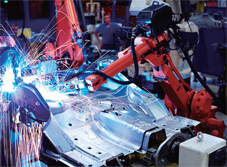
Robot laser welding has advanced into many differentindustries from automotive to electronics. It improvesautomation, providing a large return on investment (ROI),because of its flexibility, repeatability and quality. With lasers, it ispossible to weld at high speeds with great efficiency. The robot laser welding consists of a servo-controlled, multiaxismechanical arm with a laser cutting head mounted to thefaceplate of the robot arm. The cutting head has focusing opticsfor the laser light and an integral height control mechanism. Anassist gas delivery package distributes a gas, such as oxygen ornitrogen, to the welding head. Most systems use a laser generatorthat delivers the laser light to the robot cutting head through a fiberopticcable. During a weld cycle, one robot rapidly moves to the pickupposition and then compresses the mating fixture with immense force,encompassing the stampings in a die set fixture design. This designmanages the task of capturing and creating needed forces behind eachweld tab. The tooling used to pickup and compress the assembly isthen rapidly positioned in the path of the pulsed laser beam. The laser welding machine includes software that monitorswelding by measuring real-time laser energy pulses. The softwareis used as a statistical process control diagnostic tool useful fortroubleshooting welds defects. During the welding process, each of the44 spot welds is measured individually, and a part is rejected when thepulse power is 5% more or less than the specified output energy. Laser welding provides high-density energy. It is easy tocontrol and is low in heat input but deep in depth, enabling it to beused for small-area precision welding. These features make laserwelding suitable in auto and shipbuilding industry applicationsand metal-container manufacturing. Pressure and vacuum vesselsrequire high-quality, low-heat welding to ensure robustness againstmetal fatigue due to heat and pressure cycles and highly accurateassembly, low manufacturing cost, and short-term delivery.
Automation Automating welding using robots has been considered,but laser welding requires accurate alignment and direction of irradiation because of its capability ofsensitive welding. However, since laserwelding is used many times in manymodelsin small-quantity production, itis difficult to adjust its alignment by jigsand impossible to adjust its position andposture of the welded object itself in caseof welding of large vessels, thereforeit is necessary to adjust them only byrobot equipped with a welding head.Dimensional error between design data andactual welded objects and object deflectiondue to weight may cause misalignmentin the welding domain calculated fromcomputer-aided design (CAD), makingit necessary to measure the positionalrelationship between the welding head andwelded object directly. The hand-eye laser welding robot hasa welding head with two slit lasers and aCMOS camera to measure the laser focalpoint and optical axis angle of the weldedobject. Image information in laser weldingis used for monitoring in-process welding,but in-process highly accurate positioning is difficult because of the highly luminescent light generated at elevatedtemperatures, so welding is generally doneafter the welding location is detected. The welding head has an optical microscope that expands the weld targetin observation and consists of mirrorsrefracting yttrium-aluminum-garnet (YAG)laser so that its optical axis coincideswith that of the camera, i.e., visible lightgoes through the mirrors but the YAGlaser is reflected by them. The YAG laseris focused on the seam of two plates tobe butt-welded. The direction of meltingdepends on the direction of the laser抯optical axis and melting depth depends onthe positioning of focus. If the laser抯optical axis is not on the tangent plane ofthe metal plates, the direction of meltingdeviates from the weld seam as w
Zapatillas Running Baratas