A unique, one-piece, single-shot, high-performance composite pallet developed by Lomold Group of South Africa has been declared winner in the Transportation category by the JEC® (Paris) in its annual Innovation Awards Program. Lomold Group and its partners, Chuan Lih Fa Machinery Works Co. Ltd. (Taiwan), KHS Consulting cc (South Africa), and Addcomp Holland BV (the Netherlands), nominated a patented design for a long-fibre thermoplastic (LFT) pallet injection moulded in 17% fibreglass-reinforced polypropylene (PP) that was produced via a patented process developed by Lomold over the course of the last decade.
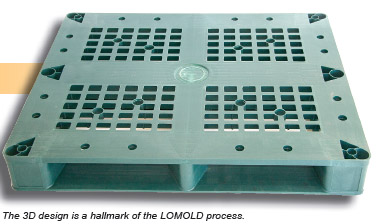
The pallet provides proof-of-concept for Lomold's new form of LFT injection moulding, which can rapidly produce large and highly complex parts with intricate design features at low shear and clamping pressures while also maintaining post-mould fibre lengths typically only seen in compression moulding. Depending on part complexity, the Lomold process produces parts whose post-mould reinforcing fibres are typically 10-50 millimetres/0.4-2.0 inches vs. 3.0-4.0 millimetres/0.1-0.2 inches for conventional LFT injection moulding. The ability to maintain fibre lengths in intricate, three-dimensional (3D) designs is a hallmark of the Lomold process, which therefore yields parts with high mechanical properties at thinner walls, lower mass, and with resulting cost-reduction opportunities. Parts with longer reinforcing fibre benefit from better low-temperature impact strength, higher mechanical properties at elevated temperatures, better dimensional stability at any wall thickness, enhanced creep and fatigue resistance-critical in a part like a pallet-and excellent surface finish. The pallet is also fully recyclable at end of service life. 10 years in the making The company has spent 10 years developing its unique variant on LFT moulding, which offers the best of both injection and compression moulding processes while helping eliminate the challenges of each. Like conventional injection moulding, the Lomold process is automated, fast-cycling, and capable of producing intricate, 3D designs with a high degree of repeatability and reproducibility (R&R). Like compression moulding, it is a cost-effective method of producing large, low-shear, low-warpage parts on lower tonnage machines while maintaining much higher post-mould fibre lengths and avoiding the design limitations of that process. For example, in compression moulding, it is difficult to achieve good glass penetration in ribs deeper than 55 millimetres/2.2 inches (owing to glass bridging), and compression moulding cannot produce parts with through-holes, which must be cut or punched out after moulding. Unless the compression tool is equipped with shear edges, such parts also require edge trimming after moulding, with each secondary operation adding time and cost to the production process. Since the Lomold process is more like conventional injection moulding, it has no trouble reproducing the pallet's multitude of ribs, holes, and angled surfaces, which help enhance product performance and reduce costs via lightweighting and one-step processing.
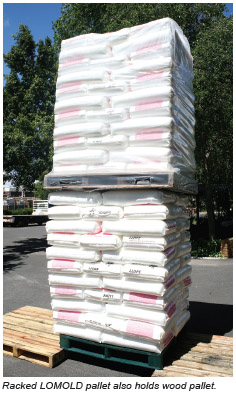
With the Lomold process, hot runners are eliminated, saving capital tooling costs and material, shortening the cooling cycle (since there are no sprues to cool and the long glass fibres help conduct heat out of the centre of the part), and eliminating the need to trim sprues. The advantages of composite pallets over wood are well known and accepted in the materials-handling and logistics industries. One important benefit is that composite pallets are tougher and less prone to breakage and damage so they require less maintenance and have longer service life-10 years on average as against 3-4 years for wood. Also, composite pallets can be repeatedly washed yet will not absorb moisture. The company plans to launch
Adidas