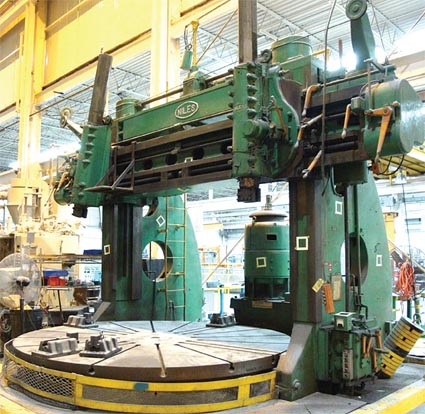
There are several considerations that need to be well-thought out when buying a vertical boring mill (VBM). But before going to the brief summary of: how much, how long and how affordable, a brief look on the principal parts: production requirements, inspection of the equipment's non-power and under power, will prepare you when you make the decision of purchasing your vertical boring mill. Vertical boring mill is important in the machining process, and is often referred to as the enlargement of a hole with the use of a drill or a cast. Several types of tools may be used in the process, ranging from single-point cutting tools to a boring head with other tools in it. This is highly commendable because it provides accurate diameter on the holes. VMB is mainly used for turning, facing or boring large workpieces that are shaped symmetrically. Because of the machine's design, circular cuts can only be made as the work is rotated against the fixed tools. The rotary table houses the mechanisms that drive it and sits on the machine's bed. Two vertical uprights are mounted to the back of the diameter of the table, which bolsters a cross rail. The cross rail can be manoeuvred up and down on the support columns in order to accommodate various workpieces. It also has one or two tool heads mounted on it, as well as each vertical upright. For smaller VBM's, there is usually one turret head and one heavy boring bar that tilts at different angles. For larger VBM's, the turret head and swivel bar are replaced by two heavy boring rams to supply vertical feed of the tools.
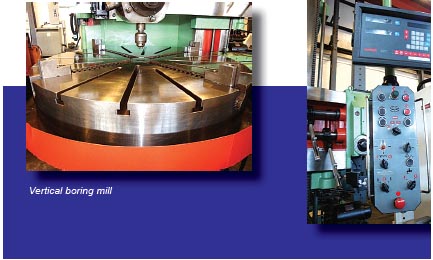
Applications for a VBM would be machining large steam engine turbine casings, ring gear blanks, locomotive tires, water turbine runners, flanges for large pipe and machine tool tables. The diameters of the workpiece may also vary. The success of the process relies upon design considerations. The so-called length-to-bore diameters are eliminated in the list since it causes the cutting tool to change its course. Through-holes are also more favoured than blind ones. The internal working surfaces must not be interrupted as well. Main parts BedA circular, hollow unit that is the main casting of the machine. It covers the spindle and the bevel gear and pinion which drives the table. TableA circular shaped casting mounted on top of the bed and is rotated through gearing. It is the workholding part comparable to the lathe's head stock and faceplate. HousingsTwo vertical members that support and rise from opposite sides of the base. The faces of the housings are finished in order to furnish bearing surfaces for the cross rail. Cross railA rectangular casting mounted on the housings to stay parallel to the surface of the table. It's counterbalanced and can be raised or lowered to accommodate various workpieces. Saddles & ToolheadsNormally VBM's have two saddle and toolhead assemblies on the cross rail. They're manoeuvred across to feed the cutting tools parallel to the table. The motion of the tools creates plane surfaces. Ram s-Similar to the cross rail, the rams are counterbalanced to aid movement in their bearings. The rams can be manoeuvred vertically in their toolheads to feed cutting tools at 90 degrees to the surface of the table. The motion of tools generates cylinders. Arch-connects the housings at the top and maintains rigidity to the structure of the machine. Selection When deciding on a machine to suit your production requirements, the user should consider a VBM over a standard lathe for the following reasons: (1) Machining a workpiece that is too large or heavy to be handled on a lathe; (2) Turning, facing and boring operations on various workpiece sizes for maximum machine flexibility; (3) Work which necessitating during setup; (4) Counterbalancing irregular or off-centre workloads for high-speed turning
Air Jordan III 3 Shoes